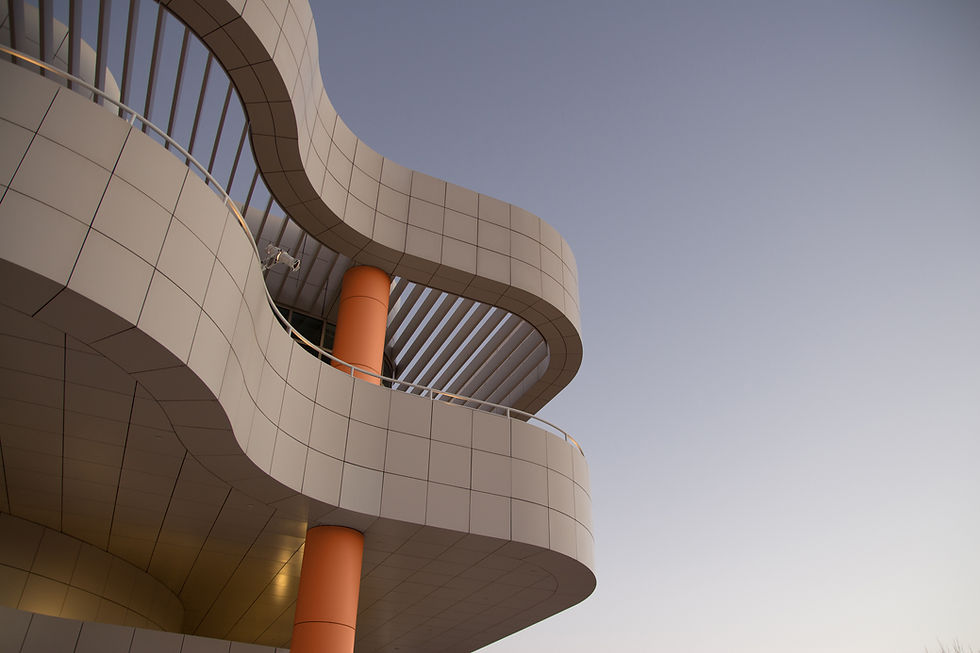
Robot welding and manual welding both have their pros and cons, and fabricators must keep these in mind when making decisions on which method to use. Robot welding is better suited to large production runs of repeatedly manufactured items, whereas manual welding is ideal for smaller runs, custom jobs, or smaller items requiring special care and attention to detail (such as TIG welded stainless).

Robot Welding
Pros:
Consistency. A correctly programmed robot is capable of producing very tidy and high quality welds with little variance in bead size or weld penetration.
Productivity. Robot welding is usually significantly faster than manual welding, allowing more product to be manufactured in the same time period.
Predictability. Once a job is programmed it will always take the same amount of time to run, unlike manual welding where there can be large variances depending on the experience of the welder and/or familiarity with the job.
Cons:
Jigging requirements. Any variances in the locations of the components or gaps between components will affect welding quality, or possibly cause a collision. This means that more extensive jigs are often required.
Setup time. The programming and jigging requirements add a lot of time to the process before the first part can be completed, which makes it unsuitable for lower quantities.
Manual Welding
Pros:
Flexibility. Design changes or custom requirements are easy to accommodate.
Setup time. Welding can commence a lot quicker at the start of the job, especially if the parts are self-jigging which reduces the need for building complex jigs. This is especially beneficial for prototypes.
Awareness. Having an experienced fabricator on the job increases the chance that any mistakes or issues from previous manufacturing processes will be noticed and dealt with before welding takes place.
Cons:
Consistency. Welding can vary depending on the fabricator on the job.
Safety. Manual welding comes with a higher chance of injury.
Speed. A robot can be a lot faster, particularly on jobs with a lot of welding required.
When ES3 consider a job for our robot welder we take into account the above points, along with details such as the minimum order quantity, order frequency, and annual usage. If you would like to learn more about our fabrication capabilities, don’t hesitate to contact the team at ES3.